Die gezielte Rundung und Glättung von Schneidkanten verbessert entscheidend die Werkzeugstandzeit und Prozessstabilität in der Zerspanung. Mechanisches Tauchgleitschleifen im OTEC Streamfinish-Verfahren nutzt abrasives Granulat und einstellbare Strömungsparameter, um materialabtragend robuste Konturen mit variablen K-Faktoren zu erzeugen. Im Gegensatz dazu basiert Electrofinish auf anodischer Metallauflösung in einem Elektrolyt, was filigrane Geometrien ohne mechanische Belastung kontaminationsfrei veredelt. Die Kombination beider Verfahren vereint hohen Materialabtrag mit extrem glatten Oberflächen für dauerhaft optimale Schnittperformance.
Inhaltsverzeichnis: Das erwartet Sie in diesem Artikel
Mechanisches Tauchgleitschleifen: Kantenhomogenisierung durch einstellbare Eintauchtiefe, Winkel und Granulatdruck
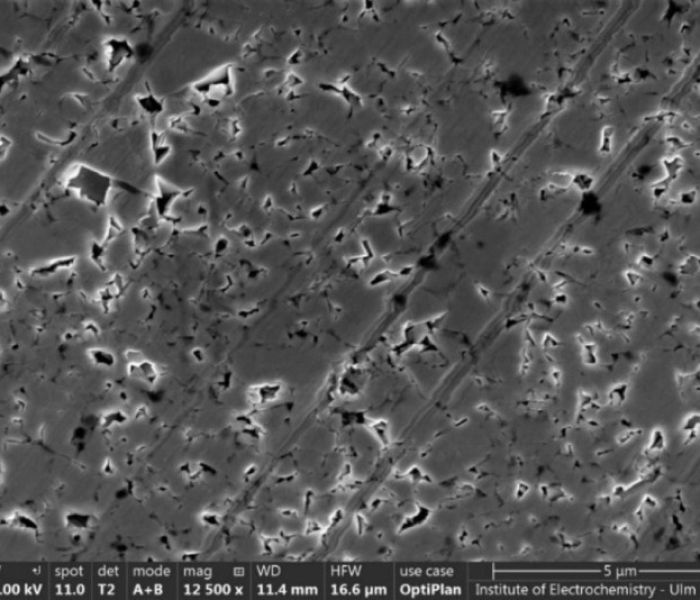
Abbildung 4 REM-Aufnahme einer elektropolierten Spanflanke (Foto: OTEC Präzisionsfinish GmbH)
Bei der Tauchgleitschleifbearbeitung im OTEC Streamfinish-Verfahren wird das Werkzeug in ein abrasives Granulatbad eingetaucht und unter Rotation einer Strömung ausgesetzt. Durch Anpassung von Eintauchtiefe, Einfallwinkel und Granulatdruck lassen sich K-Faktoren zwischen 0,5 und 2,0 realisieren. Dadurch werden Schneidkanten homogenisiert, Druckspannungen reduziert und Verfestigungen in der Randzone erzeugt, was zu optimierter Spanbildung und längeren Werkzeugstandzeiten führt. Die Modulation des Abtragsprozesses sorgt für gleichmäßige Kantengeometrien und steigert die Prozesssicherheit bei der Zerspanung.
DEM-Simulation optimiert Gleitschleifprozess durch präzise Partikelwechselwirkungen und effiziente P×V-Analysen
Die diskrete Elemente Methode (DEM) simuliert detailliert das Verhalten von Millionen einzelner Schleifpartikel und erfasst deren Wechselwirkungen mit dem Werkstück und den Behälterwänden. Über die Auswertung lokaler Druckverteilungen und Relativgeschwindigkeiten (P×V-Wert) lassen sich präzise Prozessfenster für gleichmäßige Oberflächen und optimierten Materialabtrag festlegen. Durch virtuelle Versuche verkürzen sich Entwicklungszyklen, die Reproduzierbarkeit steigt und Anwender gewinnen umfassende Kenntnisse über auftretende Kräfte sowie Biegemomente während des Gleitschleifprozesses und Energieeinsatz können detailliert analysiert werden.
Electrofinish glättet PVD-beschichtete Hartmetallwerkzeuge kontaminationsfrei auf extrem niedrige Mikrorauheit
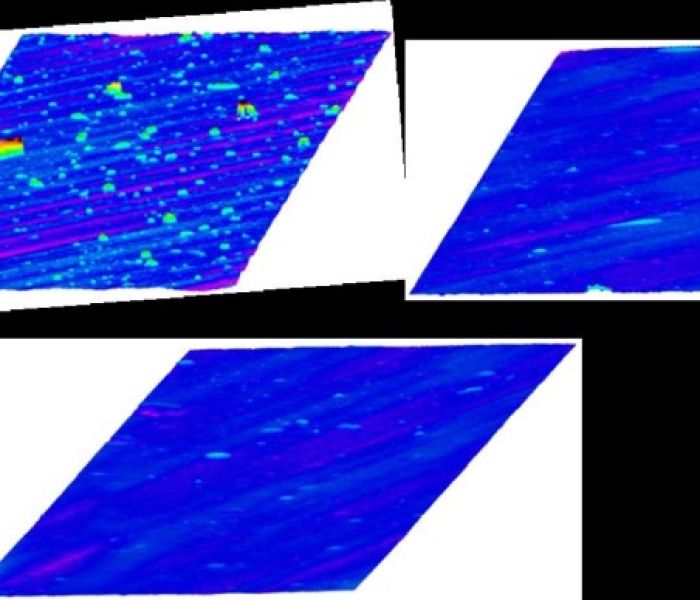
Abbildung 6 Spannfläche Gewindebohrer, Initial 0 min, Electrofinish (Foto: OTEC Präzisionsfinish GmbH)
Beim elektrochemischen Electrofinish erfolgt der Abtrag metallischer Werkstoffe anodisch in einem geeigneten Elektrolyten, vollständig ohne mechanische Beanspruchung oder abrasive Medien. Dieses Verfahren gewährleistet extrem niedrige Mikrorauheiten und erlaubt eine kontaminationsfreie Reinigung anspruchsvoller Geometrien. Insbesondere Hartmetall-Werkzeuge profitieren von einer gleichmäßigen Glättung ihrer PVD-Beschichtungen, während unerwünschtes Cobalt Leaching minimiert wird. Mit K-Faktoren zwischen 0,7 und 0,9 eignet sich das Verfahren optimal zur Erzeugung symmetrischer Kantenradien sowie präziser Wasserfall-Profile und garantiert hochreproduzierbare Ergebnisse.
Hybride Streamfinish-Electrofinish-Kombination steigert Werkzeuggenauigkeit und Oberflächenqualität im effizienten Zerspanprozess
Eine kombinierte Anwendung von Streamfinish und Electrofinish führt zu optimaler Prozesskontrolle und Oberflächenqualität. Zuerst erzeugt das mechanische Tauchgleitschleifen eine robuste Werkzeugkontur mit gleichmäßiger Makrostruktur und idealen Grundlagen für nachfolgende Beschichtungen. Anschließend glättet das elektrochemische Verfahren feinste Unebenheiten ohne mechanische Beanspruchung, entfernt Beschichtungsreste und minimiert Mikrorauheit. Diese Verkettung beider Technologien gewährleistet hohe Geometriegenauigkeit, verbesserte Schneidkantenstabilität und äußerst glatte Flanken in einem einzigen Arbeitsablauf. Diese Kombination steigert deutlich die Effizienz und Standzeit.
Kosten-Nutzen-Kalkül: Streamfinish und Electrofinish je nach Volumen und Empfindlichkeit
Streamfinish-Anlagen erfordern signifikante Investitionskosten, bieten jedoch kurze Taktzeiten und niedrige Stückkosten bei hohen Losgrößen. Robustheit und Prozessstabilität ergeben sich dank einstellbarer Parameter und starkem Materialabtrag. Electrofinish nutzt dagegen Elektrolyte und längere Durchlaufzeiten, vermeidet mechanische Belastungen und optimiert filigrane Geometrien sowie PVD-Endbearbeitung. Für Kleinserien und empfindliche Bauteile ist es besonders geeignet. Die Wahl orientiert sich an Produktionsvolumen, Werkstückempfindlichkeit, geforderter Rauheit und Wirtschaftlichkeitsfaktoren, Losgrößenvariabilität, Taktzeitoptimierung und Instandhaltungsaufwand, Standzeit, Qualitätssicherung, Flexibilität sowie Liefertermintreue.
Mechanisches Streamfinish und Electrofinish optimieren effizient Werkzeugstandzeit und Oberflächenqualität
Das OTEC Streamfinish-Verfahren ermöglicht durch gezielten Materialabtrag an Schneidkanten und einstellbare K-Faktoren robuste Werkzeuge mit optimierter Spanbildung. Electrofinish glättet feinste Geometrien kontaminationsfrei, perfektioniert PVD-Beschichtungen und minimiert Cobalt Auslaugung. Die Hybridstrategie nutzt erst mechanische Profilierung und induzierte Druckeigenspannungen, dann elektrochemische Feinbearbeitung für extrem niedrige Rauheitswerte. In Kombination steigern beide Prozesse Standzeit, Prozessstabilität und Wirtschaftlichkeit signifikant, während Werkzeugpräzision und Oberflächenqualität auf ein neues Niveau gehoben werden und reduzieren Ausschusskosten durch reproduzierbare Ergebnisse.