Die Digitalisierung ist in jedem Bereich der Wirtschaft auf dem Vormarsch. Industrie 4.0 braucht intelligente Sensoren, um die Anforderungen an automatisierte und vernetzte Fabriken zu erfüllen
Industrie 4.0: Erst durch intelligente Sensoren möglich
Die Digitalisierung ist nicht mehr aufzuhalten und beschert der Wirtschaft vernetzte und automatisierte Fabriken, die Garanten für die internationale Wettbewerbsfähigkeit Deutschlands sein sollen. Allerdings geht in der modernen Wirtschaftswelt nichts mehr ohne intelligente Sensoren. Sie sind längst kein Zukunftsprojekt mehr, sondern bereits in vielen Bereichen zu finden. Sie werden auch als Sinnesorgane der Industrie 4.0 bezeichnet und sind wie diese unverzichtbar. Eine erfolgreiche Automatisierung ist ohne Sensortechnik nicht möglich!
Intelligente Sensoren erlauben die vollständige Transparenz von Sensorfunktionen und Einstellungen der Sensoreinheiten, wobei alle Ebenen der Automatisierung berücksichtigt werden. Dies war bisher nur über umständliche Programmierungen für den Einzelfall möglich, es wiederum Echtzeit-Diagnosen und eine flexible Parametrierung der Sensorik unmöglich machte oder zumindest deutlich erschwerte.
Intelligente Sensoren, wie sie zum Beispiel in der Abstandsmessung eingesetzt werden, nehmen Werte auf, leiten dies an die Steuerung weiter oder nehmen selbst eine automatische Bewertung vor. Die gesamte Produktion lässt sich darüber steuern, wobei der große Pluspunkt die Zuverlässigkeit der Daten ist.
Mithilfe der smarten Sensorik ist es sogar möglich, den Lebenszyklus des Sensors selbst aufzuzeichnen und eine Auswertung dazu vorzunehmen. Dies wiederum wirkt sich hilfreich auf künftige Sensorentwicklungen aus, denn aus den Aufzeichnungen ergeben sich wertvolle Hinweise und Erkenntnisse.
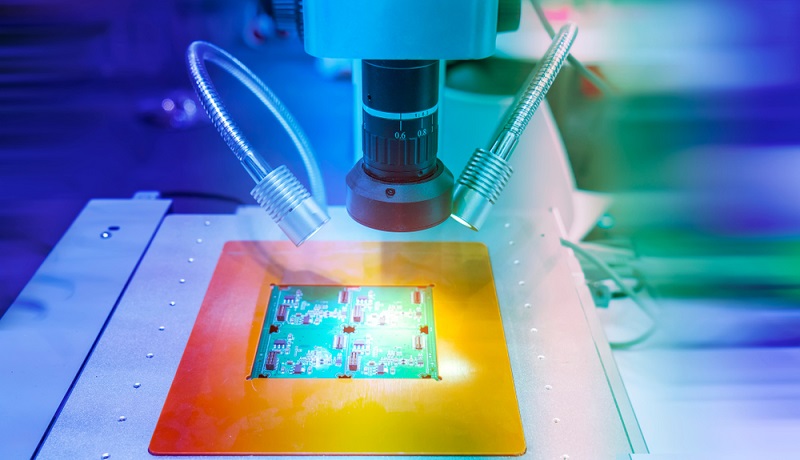
Intelligente Sensoren erlauben die vollständige Transparenz von Sensorfunktionen und Einstellungen der Sensoreinheiten, wobei alle Ebenen der Automatisierung berücksichtigt werden.(#01)
Smarte Sensortechnik in der Industrie 4.0
Smarte oder intelligente Sensoreinheiten erfassen nicht nur die verschiedenen Messgrößen, sondern bereiten auch die Signale auf bzw. verarbeiten diese. Dafür ist ein Mikroprozessor integriert, der teilweise weitere Funktionalitäten besitzt.
Intelligente Sensoren sind in der Lage, die ihnen zugedachte Aufgabe ohne weiteren Rechner auszuführen. Das heißt, sie arbeiten autonom, was zum Beispiel im Rahmen der Dezentralisierung oder der Erhöhung der Flexibilität in der Produktion wichtig ist. Um korrekt arbeiten zu können, verfügen intelligente Sensoren über verschiedene Schnittstellen.
Die Funktionsweise der Sensoren für die Industrie 4.0 ist immer gleich:
- Sensorelement nimmt die Messgröße (physikalisch oder chemisch) auf
- danach erfolgt die Weiterverarbeitung des Signals
- Endergebnis sind verwertbare Messwerte
- Umwandlung physikalischer Signale erfolgt in digitaler Elektronik
- Sensoren sind an Messverstärker angeschlossen
- durch separate Messverstärker können mehrere Funktionen gleichzeitig ausgeführt werden
Sogar kurzfristige Fehlermeldungen und -prognosen sind durch intelligente Sensoren für die Industrie 4.0 leicht zu übertragen, sodass die Produktion genau auf die Ergebnisse der Sensorik eingestellt werden kann. Teilweise kann ein Abschalten nötig sein, wenn entsprechende Meldungen vorliegen. Diese treffen meist deutlich früher ein, als sie bei einer manuellen Kontrolle herauszufinden wären.
Die moderne Sensorik erlaubt damit eine deutlich sicherere Produktion, geringere Ausfallzeiten durch Störquellen oder Fehler und eine bessere Abstimmung verschiedener Anlagen und Maschinen untereinander. Die Werkzeugmaschinen arbeiten effizienter und können besser ausgelastet werden. Eine Erhöhung der Produktionsquote bedeutet einen Wettbewerbsvorteil gegenüber der Konkurrenz.
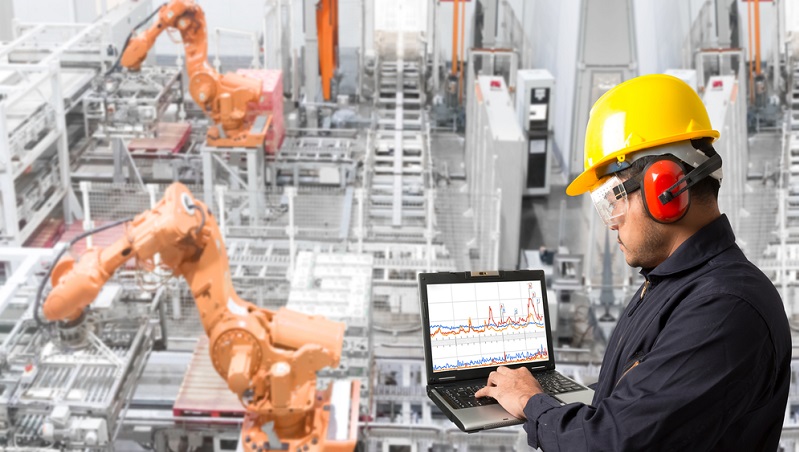
Verschiedene Modelle werden miteinander verknüpft und bilden eine virtuelle Maschine ab, deren Prozesse simuliert werden können. Der Maschinenbauer kann somit die Stabilität der Maschinen und Anlagen einschätzen und bestenfalls erhöhen.(#02)
Individualisierung oder Vereinheitlichung in der Industrie 4.0
In einer Zeit, in der jedes Unternehmen nach Individualisierung strebt, gehen doch alle den gleichen Weg: Sie gehen das Zukunftsprojekt 4.0 mit unterschiedlich großen Schritten an. Dabei wird darauf gesetzt, dass jede Komponente und Maschine innerhalb eines automatisierten Systems miteinander kommunizieren kann und dass aus jedem Unternehmen eine „Smart Factory“ zu entwickeln ist.
Intelligente Sensoren werden in der Industrie zu Sinnesorganen, die das Sehen, Hören und teilweise sogar das Fühlen übernehmen. Es werden dafür Abläufe an Maschinen beobachtet, die Prozesse werden überwacht und detektiert. Bei Überlastungen oder Fehlern wird automatisch Alarm geschlagen. Intelligente Sensoren sollen damit die Realität abbilden, eine Aufgabe, die ihnen bisher schon sehr gut gelingt. Die Daten, die von Sensoren erzeugt und ausgewertet werden, dienen der Steuerung von Maschinen und Anlagen.
Die grundlegende Aufgabe eines Sensors besteht darin, Daten aufzunehmen und nach außen zu übermitteln, was über eine feste Schnittstelle möglich ist. Doch die Schnittstellen von heute können noch mehr, als einfach nur Daten aufzunehmen und weiterzuvermitteln. Es werden weitere Daten übertragen und mit dem Sensor ausgetauscht, so zum Beispiel Daten zu Diagnose und Parametrierung im Produktionsbetrieb.
Werkzeugmaschinen sollen sich künftig selbst parametrieren oder Formate umstellen können. Diese Tätigkeit nehmen bisher noch die Mitarbeiter des Unternehmens auf manuelle Art und Weise vor, doch diese Tätigkeit ist naturgemäß fehleranfällig. Die Fehlerquote liegt bei Sensoren doch um einiges niedriger als bei einem Menschen! Der Sensor merkt auch, wenn sich Werkstücke lösen oder nicht mehr in Position liegen, schon leichte Verrutschungen sind durch die Sensoren zu erkennen.
Sie nehmen die Daten auf und verhindern durch ein rechtzeitiges Signal Beschädigungen oder Qualitätsprobleme in der Fertigung. Intelligente Sensoren überwachen alle Vorgänge lückenlos und erkennen schon vorher, ob eine Beschädigung droht. Dies lässt nicht nur Werkzeugmaschinen länger leben, sondern vermindert auch die Ausschussquote in der Produktion.
Intelligente Sensoren müssen eine Abgleich durchführen und stellen dabei Soll- und Ist-Werte gegenüber. Sie überwachen Prozesse und nutzen nicht nur vorgegebene und eingespeicherte Werte, sondern sind auch selbst lernfähig. In Zukunft ist davon auszugehen, dass sich die Sensoren nicht mehr nur auf einen Prozess begrenzen, sondern dass die Weitergabe der Daten als Hauptaufgabe gelten wird. Dementsprechend wird auch die Zahl der Sensoren steigen, wie Experten vermuten.
Damit einher wird eine Vernetzung mit ERP-Systemen gehen, sodass nicht nur die Produktionsprozesse flexibler zu gestalten sind, sondern auch Kundendaten und verschiedene Arten von Aufträgen abzugleichen sind. Diese Kopplung gibt es zwar schon, allerdings bisher nur über die Anlagesteuerung. Damit wiederum ist eine gewünschte stärkere Verbreitung der Sensordaten sowie der Informationen zur Anlage immer noch sehr aufwendig.
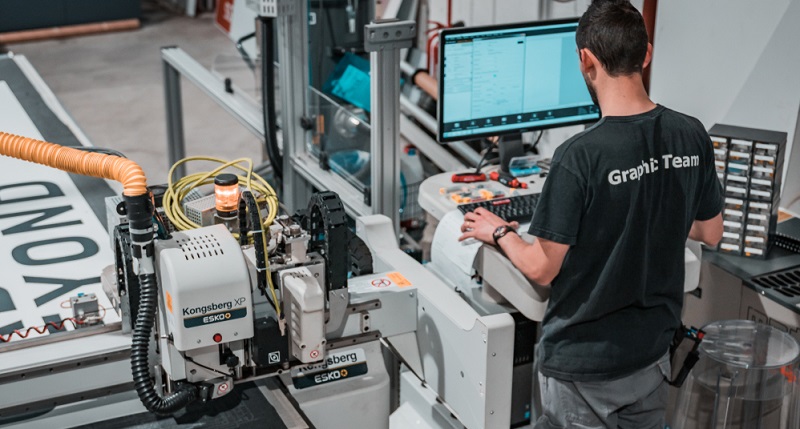
Es gibt inzwischen Studien, die belegen, dass intelligente Sensoren bzw. deren Absatzvolumen pro Jahr um bis zu 17 Prozent zunehmen.(#03)
Intelligente Sensoren in der Industrie nehmen zu
Es gibt inzwischen Studien, die belegen, dass intelligente Sensoren bzw. deren Absatzvolumen pro Jahr um bis zu 17 Prozent zunehmen. Im Zeitraum 2015 bis 2020 soll sich der Absatz auf 30 Milliarden belaufen, dafür soll sich der Preis für die Einheiten halbieren. Sicherlich spielt hier auch die zunehmende Konkurrenz eine Rolle, denn derartige Sensoren werden von immer mehr Unternehmen gebaut. Gleichzeitig wächst die Nachfrage nach Produkten, die deutlich günstiger sind als bisher. Steigt der Absatz um 17 Prozent pro Jahr, so ist davon auszugehen, dass der Preis um rund acht Prozent im Jahr sinken wird.
Wichtig ist dafür allerdings, dass die Sensoren kommunikationsfähig sind bzw. dass deren Fähigkeit dazu ausgebaut wird. Eine Komponente, die in der Industrie 4.0 funktionieren soll, muss laut Experten in der Lage sein, Daten über alle Ebenen eines Modells auszutauschen. Die Kommunikationsfähigkeit wird aber in erster Linie für die Geräte gefragt, die am Produktionsprozess mitwirken. Doch wie soll die Kommunikation in einer Welt der Industrie 4.0 aussehen? Bisher setzt die Sensortechnik auf analoge oder binäre Ausgangssignale.
Doch langsam kommt Veränderung ins Bild und mit ihr der IO-Link-Standard. Die Schnittstelle ist herstellerunabhängig und bietet eine standardisierte Kommunikation. Eine bidirektionale Kommunikation ist damit möglich. Experten sehen den IO-Link daher als sogenannte Enabling-Technologie, die für Industrie 4.0 unverzichtbar ist. Sie kann so einfach wie ein USB-Stick genutzt werden und spart Kosten oder lässt Konzepte zu Diagnose und Parametrierung bis auf die Feldbusebene umsetzen.
Des Weiteren können damit Schaltpunkte geändert oder Konfigurationen angepasst werden. Die Herkunft von Daten ist nachvollziehbar. Dennoch ist IO-Link nur eine Art und Weise, wie kleinste Sensoren Konfigurationen, Daten und Informationen weiterleiten können. Es müssen noch einige weitere Protokollvarianten hinzukommen und die Sensorik unterstützen.
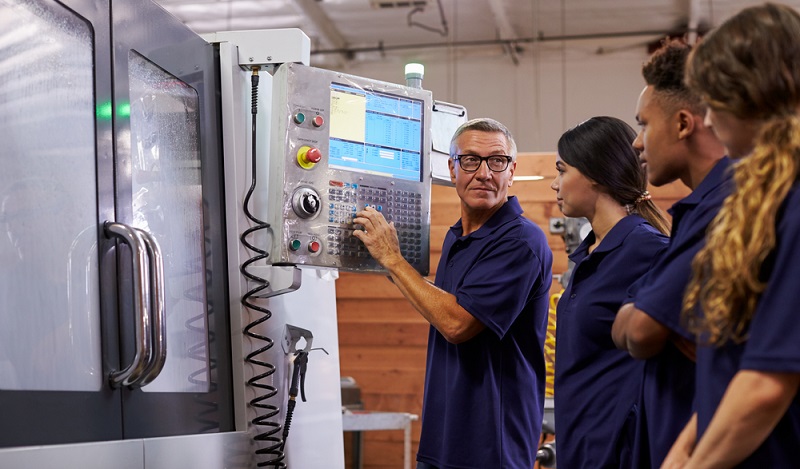
Bisher lassen sich die Möglichkeiten, die intelligente Sensortechnik für die Industrie 4.0 bieten, noch nicht vollständig nutzen.(#04)
Sensorikvorteile in der Industrie 4.0 nutzen
Bisher lassen sich die Möglichkeiten, die intelligente Sensortechnik für die Industrie 4.0 bieten, noch nicht vollständig nutzen. Denn es reicht nach Meinung von Fachleuten noch nicht aus, Mess- und Sensordaten einfach nur aufzunehmen. Daraus ließe sich immer noch keine Entscheidung treffen. Vielmehr braucht es ein mathematisches Modell zur jeweiligen Fragestellung, die gelöst werden soll. Modelle sollen dabei die Wirkzusammenhänge abbilden, die sich zwischen Zustand, Struktur und Verhalten ergeben. Sie können sich auf einzelne Bauteile und auf den Produktionsprozess selbst beziehen.
Diese Modelle lassen eine Entscheidung vorab zu treffen sein, sie können ein Verhalten des Systems bis zum gewissen Maße voraussagen. Diese Aussage zeigen Werkzeugmaschinen ganz deutlich. Die Sensorik, die sich auf Prozesse und Strukturintegration bezieht, wird zur Aufnahme von Maschinendaten verwendet.
Die Daten werden in mathematische Modelle umgewandelt bzw. in diese eingespeist und sollen eine Sammlung verschiedener Parameter ergeben, die den Zustand der Maschine oder den aktuellen Prozessstand darstellt.
Verschiedene Modelle werden miteinander verknüpft und bilden eine virtuelle Maschine ab, deren Prozesse simuliert werden können. Der Maschinenbauer kann somit die Stabilität der Maschinen und Anlagen einschätzen und bestenfalls erhöhen.
Bildnachweis:©Shutterstock-Titelbild: asharkyu -#01: asharkyu -#02: Photomontage -#03: Edward R -#04: Monkey Business Images