Die neuen Sensoren konnten sich auch ohne konventionellen pH Transmitter beweisen. Vor allem Unternehmen der chemischen Industrie tolerieren keine Abweichungen bei Messwerten.
Neues System ohne pH Transmitter hat sich bewährt
Man schrieb das Jahr 2013, als ein neues System der pH-Sensoren auf den Markt kam, das mit einem integrierten Transmitter arbeitete und die Sensorwelt auf den Kopf stellen sollte. Damit sollte der pH-Sensor zum Feldgerät werden, was ihm auch gelang. Die Smartsens-Analysesensoren konnten in zahlreichen Tests Anwender in Industrie und Forschung überzeugen.
Was waren die Gründe für die Entwicklung der Sensoren ohne herkömmliche pH Transmitter?
- Anfälligkeit der Sensoren gegen verschiedene Einflüsse durch Temperatur und Schwankungen des pH-Wertes
- ständige Neukalibrierungen der Sensoren
- Fehlerquelle Nummer eins: Signalweg bis zum pH Transmitter
- Fehlerquelle durch Integration des Transmitters ausmerzen und Umwandlung in ein 4 … 20-mA-Hart-Signal
Die bisherigen Probleme in der Prozesssteuerung mit dem Transmitter waren groß, sodass die Anwender den pH Transmitter zwar nicht entsorgen wollten, dennoch aber an der neuen Technik interessiert waren.
Vor allem die chemische Industrie zeigte sich experimentierfreudig, was für die ersten Tests sehr von Vorteil war. Immerhin stellt sie einen der Kernmärkte für die neue Technologie dar. Gleichzeitig stellt sie hohe Anforderungen, was die Präzision sämtlicher Parameter betrifft, die in die Prozessanalytik einfließen.
Des Weiteren sind die Sicherheitsaspekte zu bedenken, die in der chemischen Industrie ebenfalls eine wichtige Rolle spielen und maßgeblich bei der Auswahl neuer Technologien ist.
Die Tests wurden dementsprechend umfangreich durchgeführt und durchliefen ein scharfes Monitoring. Im Endeffekt kam dabei heraus, dass sich die neuen Sensoren ohne pH Transmitter bewähren konnten.
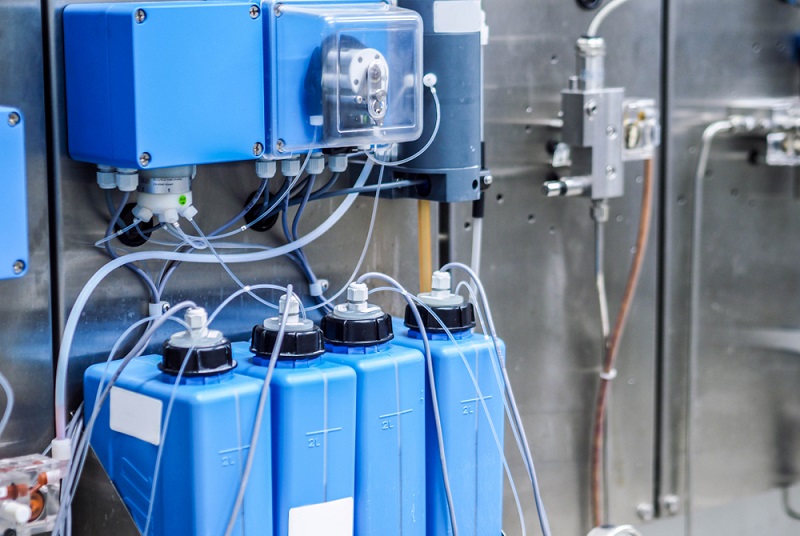
In vielen Branchen und Bereichen gilt, dass Abweichungen innerhalb eines bestimmten Maßes zu tolerieren sind und auf das Endergebnis keinen oder einen zu vernachlässigenden Einfluss haben. (#01)
Abweichungen nicht tolerierbar
In vielen Branchen und Bereichen gilt, dass Abweichungen innerhalb eines bestimmten Maßes zu tolerieren sind und auf das Endergebnis keinen oder einen zu vernachlässigenden Einfluss haben. Bei der Testung der Sensoren ohne pH Transmitter wurde daher bewusst auf Chemieunternehmen gesetzt, die hohe Anforderungen an die Messtechnik in der Analyse stellen, gleichzeitig aber auch immer geringere Toleranzen zulassen.
Die Messlatte liegt in dieser Branche besonders hoch, sollen doch möglichst alle Störfaktoren beseitigt werden, die zu einer Abweichung führen können. Getestet wurde daher in einem Versuch, wie sich ein Smartsens-pH-Sensor gegen den bisher standardmäßig eingesetzten pH Transmitter in einem Sensor schlägt.
Beide Sensoren stammten bei dem Versuch von verschiedenen Herstellern. Die Teststelle war ein Messpunkt, der üblicherweise mit einem niedrigen pH-Wert von 1,5 bis höchstens 12 (als Peak) aufwartet. Ein dauerhaft extremer Wert belastet die Sensoren extrem stark und beansprucht vor allem das Membranglas. Die einzelnen Teile altern dadurch sehr viel schneller.
Die gegebene Temperatur im Medium liegt bei 25 °C, nur selten kann sie über 40 °C ansteigen. Ein herkömmlicher Sensor weist unter Einhaltung dieser Parameter eine Standzeit von einem halben bis einem Jahr auf. Der Test sollte beendet sein, wenn die Sensoren ausfallen. Andere zeitliche Vorgaben gab es nicht.
Video: Potentiometrische pH-Messung
Sensoren ohne pH Transmitter im Test
Die Sensoren, die hier getestet werden sollten, wurden gleichzeitig eingesetzt und waren beide neu. Der analoge Sensor musste mit dem pH Transmitter direkt vor Ort kalibriert werden. Der Smartsens-Sensor wurde vor Ort überprüft, wofür Pufferlösungen eingesetzt wurden. Eine Kalibrierung war nicht nötig, denn die pH-Werte wurden immer noch korrekt angezeigt.
Sie waren zuvor beim Hersteller kalibriert worden. Jeder Sensor hat seine Daten gespeichert und bringt diese herstellerseitigen Parameter mit zum Anwender. Ein Hart-Handheld wurde zur Überprüfung der Werte genutzt. Hinzu kamen noch Datenlogger, die die dauerhafte Vergleichbarkeit aller gemessenen Werte garantieren sollten und damit einen Vergleich erst ermöglichten.
Das testende Chemieunternehmen ging davon aus, das monatlich eine Neukalibrierung direkt an der Messstelle nötig sei. Die erste Kalibrierung fand zwei Wochen nach der ersten Installation statt, beide Sensoren wurden mit Wasser gereinigt. Sie zeigen danach eine Abweichung von 0,1 pH und wurden in den Pufferlösungen pH 4 und 7 getestet. Danach erfolgt das Kalibrieren.
Einen Monat später fand eine erneute Überprüfung statt, die Abweichungen lagen hier bei 0,05 pH, teilweise sogar noch weniger. Die Werte wurde bei beiden Sensoren gemessen. Die Verantwortlichen zeigten sich damit zufrieden, was auch acht Wochen nach der ersten Inbetriebnahme der Geräte noch der Fall war. Abweichungen oder Ausfälle waren nicht feststellbar bzw. nicht nennenswert.
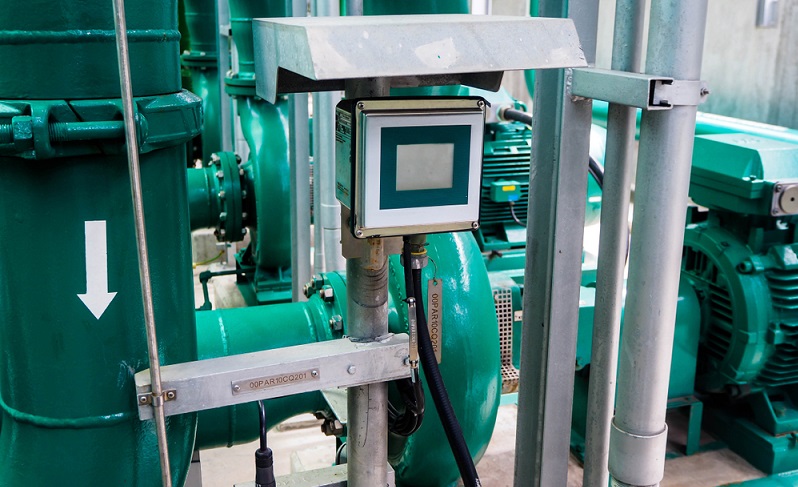
Die neuen Sensoren ohne konventionellen pH Transmitter konnten auch Skeptiker überzeugen und zeigten sich mit all ihren Vorteilen in dem doch recht umfangreichen Test. (#02)
Vorteile der neuen Technologie
Die neuen Sensoren ohne konventionellen pH Transmitter konnten auch Skeptiker überzeugen und zeigten sich mit all ihren Vorteilen in dem doch recht umfangreichen Test. Ein großer Vorteil ist zum Beispiel dass die Vorgaben, die seitens des Unternehmens an die Analysemessstellen gestellt werden, mit den neuen Sensoren besser umsetzbar sind.
Für viele dieser Messstellen sind klare Vorgaben vorhanden, mit denen Abweichungen geregelt werden. Doch gerade diese Abweichungen sind in einem derart kleinen Toleranzbereich, dass sie beinahe schon als nicht vorhanden bezeichnet werden können. Die Prozesssicherheit ist das A und O, gerade in der chemischen Industrie!
Viele elektrochemische Sensoren altern besonders schnell, weil sie hohen Belastungen durch die Umwelt ausgesetzt sind. Hier wirken Temperatur und Feuchtigkeit auf sie ein, auch das Messmedium ist entscheidend für die Alterung der Sensoren. Teilweise ist ein tägliches Kalibrieren nötig, manchmal sogar ein täglicher Austausch.
Bei einer Kalibrierung vor Ort, bei der Pufferlösungen eingesetzt werden, sind die vorgegebenen Genauigkeiten nicht einzuhalten, denn diese Lösungen altern und verschmutzen selbst. Sie sind Sauerstoff und CO2 ausgesetzt, haben eine unterschiedliche Leitfähigkeit und gelten damit als unsichere Referenzen. Die Kalibrierung der Sensoren muss daher im Labor stattfinden, was oft nicht möglich ist, da die Speicherung der Daten nicht oder nur unzureichend funktioniert.
Smartsens bietet die Lösung und offeriert einen integrierten pH Transmitter, der deutlich weniger anfällig ist und eine große Erleichterung für die Arbeit an den Messstellen darstellt. Die Sensoren können praktisch offline kalibriert werden, wobei die Idee hinter der Erfindung war, dass pro Messstelle zwei Sensoren eingesetzt werden.
Ein Sensor befindet sich bei der Kalibrierung im Labor und speichert die entsprechenden Daten. Der andere ist für die Messung eingesetzt, beide können in verschiedenen Intervallen ausgetauscht werden. Reinigungs- und Pufferlösungen sind damit tabu, es muss auch keine weitere Ausrüstung für das Kalibrieren an den Messstellen vorhanden sein. Die Sensoren werden vor Ort gewechselt, die übrige Arbeit findet im Labor statt.
Video: PH Messgerät kalibrieren einstellen und messen
Transmitter gelten als Achillesferse
Die neuen Sensoren ohne herkömmlichen pH Transmitter sind eine Alternative zu den althergebrachten Sensoren, die in jedem Monitoring zeigten, dass sie den Anforderungen nicht gewachsen waren. Der pH Transmitter galt schon lange als Achillesferse des gesamten Systems und das, obwohl seit Jahren Sensoren mit integrierten Speichern auf dem Markt vorhanden sind.
Die Kalibrierung aus dem Labor konnte hier immer gespeichert werden, dennoch wurde ein externer pH Transmitter benötigt. Das Risiko einer falschen Kalibrierung sollte damit gesenkt werden.
Der Aufbau der Messstelle blieb jedoch immer gleich:
- Sensor
- Verbindungskabel
- pH Transmitter
Der Aufbau war zwar immer gleich, nicht jedoch die Fehlerquellen. Sie waren zahlreich und variierten je nach Versuchsaufbau. Die Erklärung dafür: Wird der pH-Wert gemessen, handelt es sich um eine hochohmige Messung, bei der eine Spannung zwischen – 400 und 400 mV erzeugt wird. Die analogen Signale müssen über doppelt geschirmte Kabel an den Transmitter übermittelt werden, dort wird der Spannungswert gewandelt.
Nun erfolgt die Umrechnung in den später angezeigten pH-Wert. Die Kompensation der Temperatur wird dabei über Temperaturfühler sichergestellt. Die meisten Hersteller richten ihre Sensoren so ein, dass hier nur analoge Signale ankommen, die intelligente Verarbeitung der Signale erfolgt erst im Transmitter.
Viele Jahre lang forschten die Experten daran, das Problem der Hochohmigkeit durch neue Entwicklungen von Steckern und Kabeln zu verbessern oder sogar auszumerzen. Auch neue Schaltungstechniken kamen zum Einsatz, deren Leitfähigkeit ständig überprüft und verbessert wurde. Dennoch konnte das Problem der Anfälligkeit der Transmitter nicht zufriedenstellend gelöst werden. Wurden digitale Sensoren eingesetzt, musste sogar eine mehrfache Wandlung der Signale erfolgen, was wiederum zu neuen Fehlerquellen führte.
Jede Fehlerberechnung zeigte, dass der pH Transmitter Ursache der meisten Fehler war, wenngleich der Signalweg nur ein Teil der Problemstellung war. Auch die falsche Installation, eine fehlerhafte Konfiguration und Verdrahtung sorgten dafür, dass der Transmitter nicht fehlerfrei arbeiten konnte. Um diese Fehler zu verbessern, musste stets ein hoher Aufwand für Überprüfung und Wartung einkalkuliert worden, teilweise bis zu 300 Minuten im Jahr pro Transmitter.
Der Zeitaufwand rührte aus der nicht standardisierten Bedienung und der Wichtigkeit, die Werte bis zur Leitstelle zu überprüfen. Anwender kamen zu dem Schluss, dass Analyse gleichbedeutend mit Aufwand sei und unrecht hatten sie damit nicht!
Smartsens war nun in der Lage, die genannten Fehlerquellen zu eliminieren, da die Umwandlung der Signale auf den geforderten Wert 4 … 20 mA im Steckkopf stattfindet. Dieser ist komplett vergossen und geschirmt, unterliegt damit keinen Einflüssen durch Sauerstoff, CO2, Strahlung, Staub oder anderen Umweltfaktoren. Außerdem können die Sensoren direkt mit dem Prozessleitsystem verbunden werden. Ein zusätzlicher Service durch den Hersteller ist nicht mehr nötig!
Sicherheit als Maßgabe
Kein reiner Service, sondern eine Frage der Sicherheit: Der integrierte Transmitter sorgt dafür, dass die Sicherheit für die Anwender so hoch wie möglich bleibt. Dies war bisher nicht gegeben bzw. schränkten Sicherheitsvorgaben die Messtechnik ein.
Die neue Technik hingegen macht es möglich, dass eine komplette Messstelle in Zone 0 eingerichtet werden kann, wobei diese Zone die explosionsgefährdeten Bereiche beschreibt. Ein externer Transmitter konnte bislang nur bis zur Zone 1 eingesetzt werden. Der gesamte Aufbau wird nun vereinfacht. Die Bedienung der neuen Sensoren überzeugt in ihrer Einfachheit über übliche Hart-Handheld-Geräte.
Fazit: Die Anwender loben die einfache Bedienbarkeit der Sensoren, die ohne aufwendige Einarbeitungszeit genutzt werden können. Die Anwendung ist praktisch identisch mit den bisher verwendeten Sensoren, nur sicherer, einfacher und mit geringeren Abweichungen.
Bildnachweis:©Shutterstock-Titelbild: engineer story-#01: engineer story-#02: engineer story