Der Wettbewerbsdruck steigt und die Rahmenbedingungen für Unternehmen werden immer härter: Sie müssen sich heutzutage mit internationalen Mitbewerbern messen sowie mit steigenden Preisen und Rohstoffknappheit herumschlagen. Dazu kommen immer höhere Anforderungen seitens der Kunden.
Um dennoch langfristig wettbewerbsfähig zu bleiben, ist es daher essentiell, laufend Produktionsprozesse zu evaluieren und zu verbessern. Das klingt in der Theorie sehr einfach, doch in der Praxis stellt dieses Vorhaben viele Unternehmen vor große Herausforderungen. Erfolgsentscheidend ist vor allem die richtige Vorgehensweise, wie der folgende Artikel verrät.
Inhaltsverzeichnis: Das erwartet Sie in diesem Artikel
Prozessoptimierung in Industrie und Produktion: Worum geht es genau?
Zunächst ist es hilfreich, zu definieren, was ein Produktionsprozess genau ist. In der Praxis versteht man darunter einen standardisierten Arbeitsablauf. Dabei werden mit bestimmten Fertigungsverfahren und Arbeitsmitteln Rohstoffe oder Zwischenprodukte maschinell oder manuell bearbeitet. Als Arbeitsmittel gelten beispielsweise Maschinen, technische Anlagen und Werkzeuge.
Anders formuliert werden beim Produktionsprozess materielle Güter wie Rohstoffe und fertige Komponenten mit immateriellen Gütern (zum Beispiel menschliche Arbeitsleistung) so kombiniert, dass daraus ein gewünschtes Produkt entsteht.
Das Ziel eines solchen Prozesses ist es jedenfalls, ein fertiges Produkt zum Verkauf herzustellen.
Dabei gilt es die folgenden Faktoren zu beachten:
- Die Qualitätsvorgaben müssen eingehalten werden.
- Die Durchlaufzeiten sollten so gering wie möglich sein. Das bedeutet auch, Bestände gering zu halten und für kurze Wiederbeschaffungszeiten zu sorgen.
- Die Wirtschaftlichkeit muss stets gegeben sein. Deshalb ist es wichtig, auf die optimale Auslastung der Anlagen zu achten und die Kosten zu minimieren.
Diese drei Faktoren können nie isoliert betrachtet werden, sondern stehen stets in Wechselwirkung zueinander. Wer seinen Kunden beispielsweise bestimmte Liefertermine garantiert, muss dabei zeitgleich sowohl auf die Qualität der Rohstoffe als auch auf die rechtzeitige Zulieferung achten.
Bei der Prozessoptimierung in der Produktion geht es nun darum, die bestehenden Abläufe zu verbessern. Dabei stehen vor allem die drei genannten Faktoren und deren Abhängigkeitsverhältnis zueinander im Mittelpunkt. Die große Herausforderung ist es, jeweils die richtige Mischung in puncto Qualität, Durchlaufzeiten und Wirtschaftlichkeit zu erreichen. Dafür stehen zwei unterschiedliche Vorgehensweisen zur Verfügung.
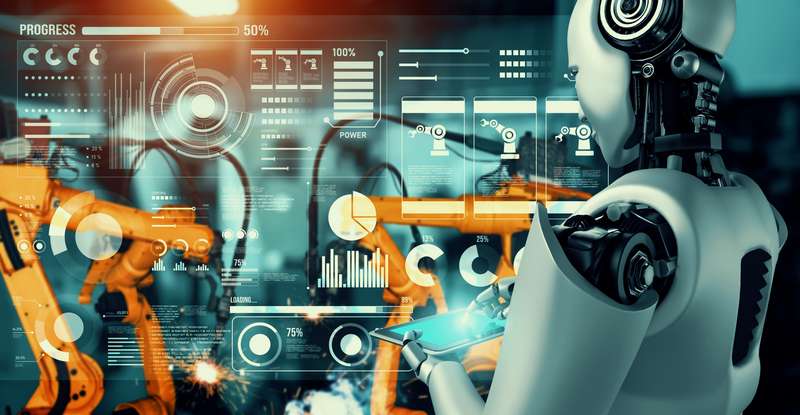
Bei der Prozessoptimierung in Industrie und Produktion gibt es keine einheitliche Vorgehensweise. Ein meist gravierender Unterschied zwischen IST- und SOLL-Zustand dient als Ausgangsposition. ( Foto: Shutterstock- Blue Planet Studio_)
Prozessoptimierung: Der sanfte und der radikale Ansatz
Egal, welcher Ansatz gewählt wird: Am Beginn einer jeden Prozessoptimierung gilt es zunächst, den IST-Zustand der zu optimierenden Abläufe zu analysieren. Danach werden Überlegungen angestellt, wie der Idealzustand aussehen könnte – der entsprechender SOLL-Zustand des Prozesses wird skizziert. So wird schnell sichtbar, an welchen Schrauben gedreht werden muss, um möglichst rasch vom aktuellen IST- zum gewünschten SOLL-Zustand zu kommen.
Nun gibt es zwei Methoden: Zum einen können die bestehenden Prozesse in laufenden kleinen Schritten optimiert werden. Im asiatischen Wirtschaftsraum wird dafür der Begriff Kaizen verwendet. Das Wort setzt sich aus „Kai“ für „Veränderung“ und „Zen“, was so viel bedeutet wie „zum Besseren“, zusammen. Die Japaner beziehen sich mit Kaizen jedoch nicht nur auf Prozessoptimierungen, sondern sehen dies vielmehr als ganzheitliche Unternehmensphilosophie.
In Europa hat sich dafür seit den 1990er-Jahren der Begriff „Kontinuierlicher Verbesserungsprozess“ (KVP) etabliert. Grundsätzlich handelt es sich dabei genau wie bei Kaizen um die stetige Verbesserung von Prozessen. Die Europäer gehen das Thema jedoch wesentlich nüchterner an und haben dabei oftmals vor allem die Kostenoptimierung bestehender Prozesse im Sinn.
Eine weitaus radikalere Vorgehensweise ist das sogenannte „Business Process Reengineering“. Dabei werden bestehende Prozesse gänzlich eingestampft und durch neue ersetzt.
Beide Varianten haben ihre Vor- und Nachteile. Welche Vorgehensweise im jeweiligen Fall besser geeignet ist, zeigt sich in den meisten Fällen nach der Gegenüberstellung des IST- und SOLL-Zustandes. Sind zur Erreichung des SOLL-Zustandes nur ein paar kleine Änderungen erforderlich, bietet sich die sanfte Vorgehensweise an. Gibt es hingegen einen größeren Gap, könnte der radikale Ansatz sinnvoller sein.
Eines ist dabei zusätzlich zu berücksichtigen: Der Industrieprozess beginnt und endet nicht bei der jeweiligen Maschine, sondern umfasst weitaus mehr. So sollten Firmen auch Komponenten wie das Produktionsgebäude selbst oder die verwendeten Tore oder Verladesysteme unter die Lupe nehmen – die gesamte umliegende Infrastruktur spielt eine Rolle.
So kann sich zum Beispiel die Installation eines neuen Tors auf eine Vielzahl von Produktionsprozessen positiv auswirken, da so die Durchlaufzeiten entscheidend reduziert werden können.
Video: Was ist BPM (Business Process Management)?
Die wichtigsten vier Ziele der Prozessoptimierung
Bei der Optimierung von Industrieprozessen werden meist die folgenden vier Ziele angestrebt:
- Qualitätsverbesserung
- Produktivitätssteigerung
- Durchlaufzeiten verkürzen
- Ressourceneinsatz reduzieren
Wie bereits erwähnt, entstehen zwischen diesen Zielen Wechselwirkungen. Dennoch ist es sinnvoll, sich bei der Verbesserung der Prozesse zunächst auf ein bestimmtes Ziel zu konzentrieren. Gleichzeitig sollten Firmenchefs jedoch auch die anderen Aspekte nicht völlig aus dem Blickfeld verlieren. Doch welche Möglichkeiten stehen dafür jeweils zur Verfügung?
Qualitätsverbesserung
Um den qualitativen Output zu erhöhen, kommt oftmals die sogenannte „Six-Sigma-Methode“ zur Anwendung. Dabei handelt es sich um ein systematisches Vorgehen, das sich von anderen Maßnahmen durch seinen mathematischen Ansatz unterscheidet.
Die fünf Phasen der Six-Sigma-Methode werden im DMAIC-Zyklus beschrieben:
- Define (D): Was ist das Problem und welches Ziel wird angestrebt?
- Measure (M): Welche Performance bietet der IST-Prozess?
- Analyze (A): Was sind die Kernursachen für das Problem?
- Improve (I): Wie lässt sich das Problem beseitigen?
- Control (C): Wie kann die Verbesserung in der Organisation verankert werden?
In der Define-Phase sollte auch das Feedback von Kunden Berücksichtigung finden. In der Improve-Phase gilt es zu überlegen, wie diese Vorstellungen effizient und wirtschaftlich erfüllt werden können.
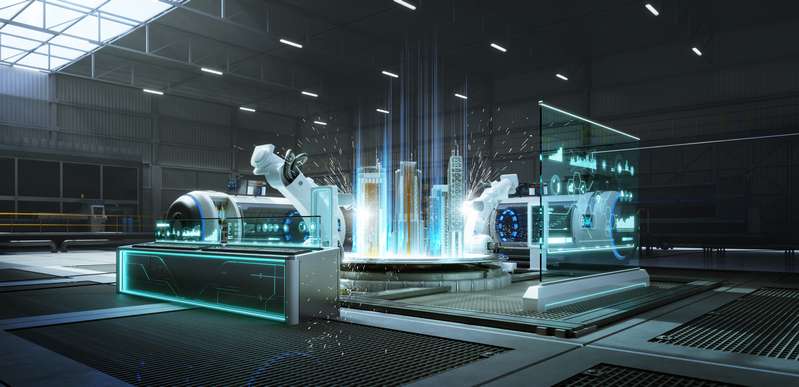
Verbessern oder erneuern? In manchen Fällen ist es sinnvoller und wirtschaftlicher, den Prozess nicht in kleinen Schritten zu verbessern, sondern ihn komplett neu aufzusetzen. ( Foto: Shutterstock- jamesteohart_)
Produktivitätssteigerung
Im Zusammenhang mit der Steigerung der Produktivität ist Industrie 4.0 ein großes Schlagwort. Im Mittelpunkt steht hier in erster Linie die Automatisierung von Produktionsabläufen. Zu berücksichtigen ist dabei allerdings, dass die geplanten Anschaffungen auch wirtschaftlich sein müssen. Das ist nur dann der Fall, wenn die Vorrichtungen und Maschinen wirklich sehr oft verwendet werden.
Doch es gibt nicht nur technische Möglichkeiten, um die Produktivität zu steigern – auch organisatorische Maßnahmen können dabei eine wichtige Rolle spielen. Um Abläufe zu verbessern, kommt dabei oftmals die „5S-Methode“ zur Anwendung. Die einzelnen „S“ stehen für folgende Begriffe:
- Seiri: Sortieren
- Seiton: Setzen (beziehungsweise: Anordnen)
- Seiso: Sauberkeit
- Seiketsu: Standardisierung
- Shitsuke: Selbstdisziplin
Das grundsätzliche Motto lautet: Was nicht gebraucht wird, kommt weg. Dadurch können Verschwendungen schnell erkannt und eliminiert werden. Darüber hinaus werden Vorbereitungs- und Rüstzeiten verringert und dadurch die Produktivzeiten von Maschinen erhöht.
Durchlaufzeiten verkürzen
Eine der häufigsten Methoden, die zur Verkürzung der Durchlaufzeiten angewendet wird, ist die sogenannte Wertstromanalyse. Dabei wird nicht nur der Materialfluss, sondern auch der Informationsfluss analysiert.
Das Ziel dabei ist es, eine sinnvolle Verknüpfung aller Prozesse zu erreichen. Dadurch verringert sich nicht nur die Durchlaufzeit, sondern darüber hinaus werden auch Materialbestände und mögliche Fehler reduziert.
Die Analyse erfolgt in den folgenden Schritten:
- Analysebereich definieren und eingrenzen
- Expertenteam zusammenstellen
- Bestehende Prozessschritte ermitteln
- Kennzahlen zu den einzelnen Schritten definieren und sammeln
- Die Prozesse auf einer Wertstrom-Karte visualisieren
- Vorhandene Prozessdaten auswerten
- Die Schwachstellen beseitigen und Verbesserungspotenziale realisieren
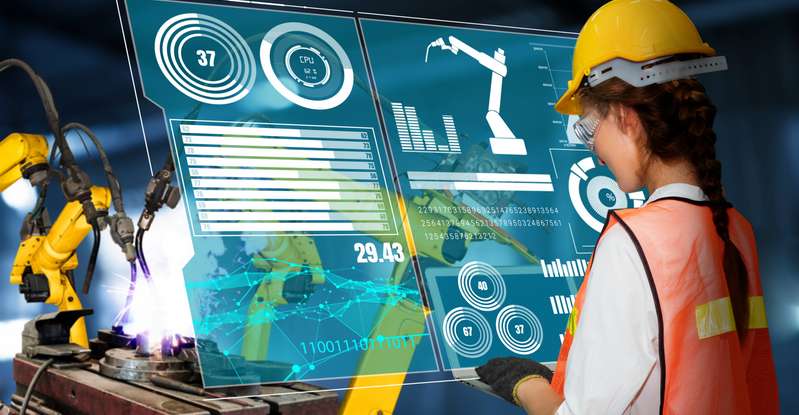
Egal, welcher Ansatz gewählt wird: Am Beginn einer jeden Prozessoptimierung gilt es zunächst, den IST-Zustand der zu optimierenden Abläufe zu analysieren. ( Foto: Shutterstock- Blue Planet Studio )
Beim Einsatz der Ressourcen hat sich die Methodik der „Lean Production“ etabliert. Dabei geht es um einen effizienten und sparsamen Einsatz von Werkstoffen, Personal und Arbeitsmitteln.
Vor allem drei Dinge, die wertvolle Ressourcen binden, sollen mit Hilfe der „Lean Production“ verhindert werden:
- Überproduktion
- Lange Durchlaufzeiten
- Fehlerhafte Produkte
Die „Just-in-Time-Produktion“ spielt dabei oftmals eine essentielle Rolle. Dabei handelt es sich um eine Produktionsstrategie, bei der das für die Produktion erforderliche Material genau in jener Menge und zu jenem Zeitpunkt angeliefert wird, wenn es benötigt wird. Dazu müssen Einkauf, Logistik, Produktion und Vertrieb entsprechend koordiniert werden.
Entscheidend für den Erfolg dieser Strategie ist die zuverlässige Kommunikation mit allen Beteiligten. Bei automatisierten Systemen erfolgt diese über eine Schnittstelle, die das Lagerverwaltungssystem des Lieferanten und die interne Produktionsplanung verbindet.