Herkömmliche Schmiedewerkzeuge haben ihre Grenzen. Bisher ist es nicht möglich, so genannte Hinterschnitte auszuformen. Das sind Aussparungen oder Vorsprünge senkrecht zur Ausformrichtung. Ein Beispiel dafür ist die Aussparung für die Bolzenbohrung bei Stahlkolben für Fahrzeugmotoren. Bislang muss diese Bohrung nachträglich ausgeführt werden. Im Rahmen des Forschungsprojekts „Hinterschnittschmieden“ haben Wissenschaftler des in Hannover ansässigen Institut für Integrierte Produktion (HPI) Hannover gGmbH dieses Problem nun gelöst.
Werkzeug-Demonstrator auf der Hannover Messe
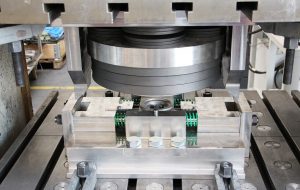
Dieses Schmiedewerkzeug erzeugt Hinterschnitte. Bei der Hannover Messe wird es als Modell zu sehen sein.
Auf der vom 24. bis 28. April 2017 statt findenden Hannover Messe stellen sie ihre Neuentwicklung vor. Ihr Demonstrator zeigt, wie die Vorbohrung für die Bolzen bereits beim Schmieden des Bauteils ausgeführt werden können. Das neue Werkzeug macht diese Hinterschnitte möglich, indem es sie bereits während des Schmiedens ausführt. Dazu verfügt das Werkzeug neben der zweiteiligen Hohlform für das neue Motorteil über zwei bewegliche Stempel.
In diese zweiteilige Hohlform, das so genannte Gesenk, ist die Geometrie das zu schmiedenden Bauteils eingraviert. Sobald sich das Gesenk schließt, fahren die Stempel aus und pressen sich horizontal in den heißen Stahl. Dadurch erzeugen sie die Hinterschnitte, in diesem Fall die Aussparungen für die Bolzenbohrung. Sobald sich das Gesenk öffnet, kann das fertige Motorbauteil entnommen werden.
Vorteile des Hinterschnitt-Schmiedens
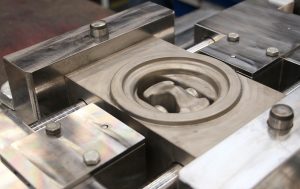
Das Werkzeug verfügt über seitliche Stempel. Wenn sich das Gesenk schließt, fahren sie aus und erzeugen die Vorbohrung für den Kolbenbolzen.
Das Hinterschnittschmieden macht die dann folgende Nachbearbeitung leichter und spart somit Zeit. Außerdem spart es Energie, weil rund fünf Prozent weniger Material für einen neuen Stahlkolben benötigt werden, wenn die Vorbohrungen schon während des Schmiedens eingebracht wird. Die Stahlkolben lassen sich also nicht nur schneller, sondern auch umweltfreundlicher und günstiger produzieren. Die Wissenschaftler des IPH erwarten, dass die mit dem Hinternschnittschmieden produzierten Komponenten belastbarer und widerstandsfähiger sind. Denn bisher müssen die Vorbohrungen nach dem Schmieden spanend hergestellt werden, was den natürlichen Faserverlauf des Materials unterbricht. Die Umformung durch das Werkzeug zum Hinterschnitt-Schmieden nutzt den Faserverlauf dagegen aus.
Die IPH-Wissenschaftler haben das Werkzeug zusammen mit Industriepartnern entwickelt. Die Technologie nutzt das so genannte ‚mehrdirektionale Umformen‘, das am IPH seit über zwanzig Jahren erforscht wird. Für Kurbelwellen hat das Institut diese Technologie bereits zur Anwendungsreife gebracht. Die Forscher haben sich zunächst auf Kolben aus hochfestem Stahl für kleine Turbo-Motoren konzentriert, aber das Prinzip lässt sich auch auf andere Komponenten übertragen.
Bildnachweis: © alle IPH